The Ultimate Guide to Plastic Injection Molding Supplies
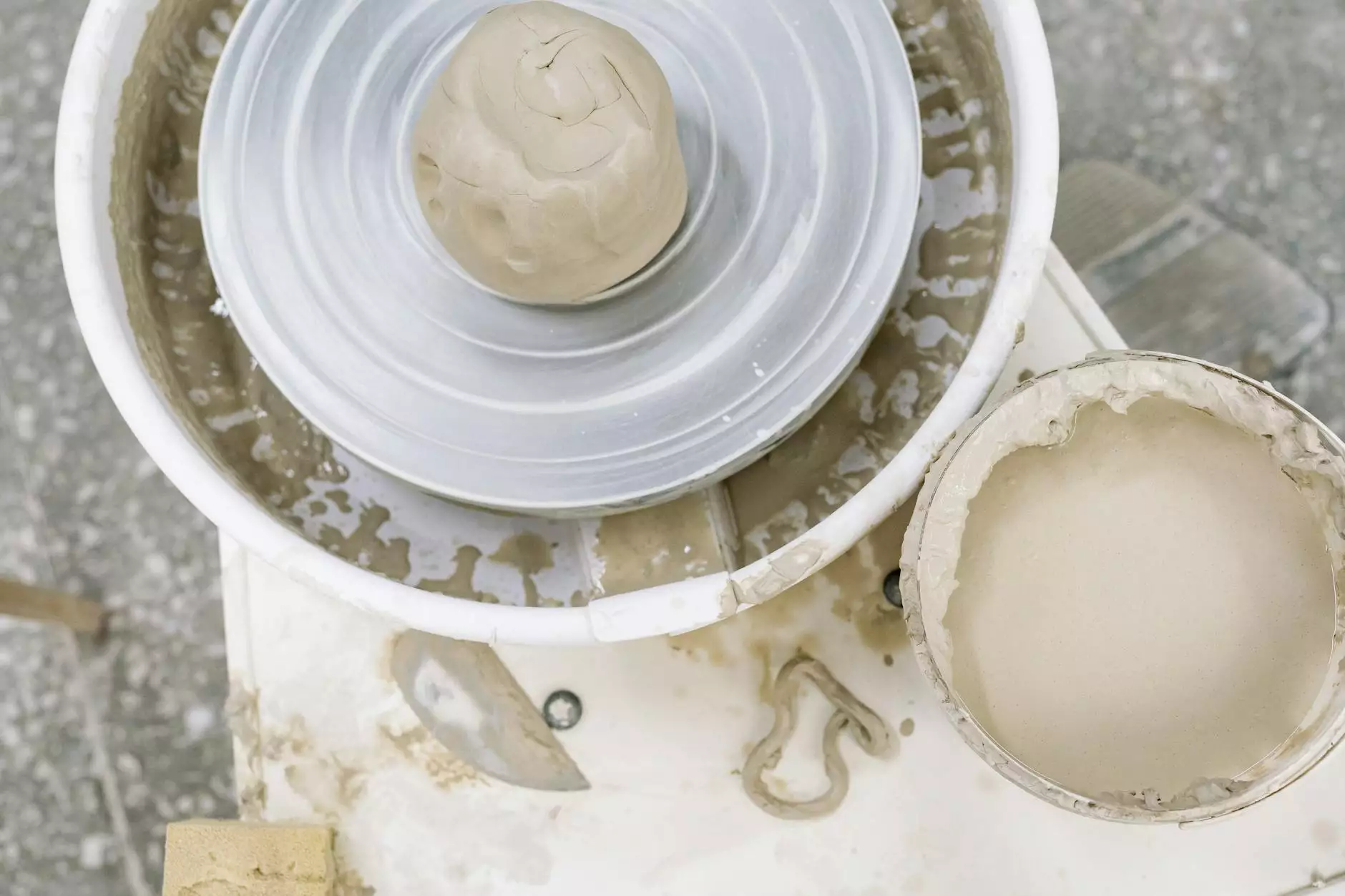
In the dynamic and ever-evolving world of manufacturing, plastic injection molding stands out as a cornerstone process that enables the production of a myriad of intricate components with precision and efficiency. To enhance operational excellence, understanding plastic injection molding supplies is imperative for any business involved in this field. In this guide, we will delve into the intricacies of plastic injection molding supplies, what they encompass, their significance in the manufacturing process, and how they can be leveraged to optimize production.
Understanding Plastic Injection Molding
Before we explore the specifics of plastic injection molding supplies, it is essential to grasp the fundamental process of plastic injection molding itself. This manufacturing technique involves the injection of molten plastic into a mold cavity, where it cools and solidifies to take on the desired shape. The versatility and adaptability of this process allow it to be applied across various industries, including:
- Automotive
- Consumer Goods
- Medical Devices
- Electronics
- Toys
The efficiency of this method not only reduces material waste but also increases production speed, making it a preferred choice for mass production.
Core Components of Plastic Injection Molding Supplies
To engage in plastic injection molding effectively, several key supplies are necessary. Each component plays a vital role in ensuring that the production process runs smoothly and produces quality products. Here's a breakdown of essential plastic injection molding supplies:
1. Injection Molding Machines
At the heart of the injection molding process is the injection molding machine. These machines are classified into two main categories:
- Hydraulic Machines: Known for their high clamping force, hydraulic machines are widely used for large and complex parts.
- Electric Machines: These machines are more energy-efficient and provide greater precision, making them ideal for smaller, intricate products.
2. Molds
The mold is the critical component that shapes the molten plastic into the desired form. Molds can be custom-designed for specific applications, and they come in various types:
- Single-Cavity Molds: Produce one part per cycle.
- Multi-Cavity Molds: Can produce multiple parts simultaneously, enhancing productivity.
- Family Molds: Allow the simultaneous production of different parts in a single cycle.
Quality molds significantly affect the production cycle time and the overall quality of the finished product.
3. Raw Materials
Choosing the right raw materials is crucial for the success of plastic injection molding. The most common materials used include:
- Thermoplastics: Such as ABS, polypropylene, and polystyrene, these materials are widely favored due to their versatility and ease of processing.
- Thermosetting Plastics: These materials, once cured, cannot be reshaped, making them ideal for specific applications requiring high thermal resistance.
- Elastomers: Known for their flexibility and resilience, elastomers are used in products where flexibility is key.
The Importance of Quality Plastic Injection Molding Supplies
The role of quality supplies cannot be overstated in the injection molding process. Low-quality materials and equipment can lead to numerous challenges, including:
- Increased Production Costs: Poor-quality materials can result in more defects, requiring costly rework or waste.
- Longer Lead Times: Inefficient machines and molds can slow down production cycles.
- Diminished Product Quality: The final product may not meet industry standards, affecting the brand's reputation.
Thus, investing in high-quality plastic injection molding supplies is essential for enhancing productivity and ensuring customer satisfaction.
Finding Reliable Plastic Injection Molding Supplies
With the increasing demand for plastic products, many suppliers emerge in the market. However, finding a reliable supplier for plastic injection molding supplies can be challenging. Here are some key factors to consider:
1. Reputation and Experience
Look for suppliers with a solid reputation and a proven track record in the industry. Established suppliers are likely to have extensive experience and can offer insights into best practices.
2. Product Quality
Quality should always be the priority. Request material certifications and samples to assess the quality before making a purchase.
3. Customer Support
Exceptional customer support is crucial for resolving queries and issues promptly. A supplier that offers comprehensive support helps ensure smooth communication throughout the process.
4. Price and Availability
While price is a consideration, it should not be the only factor. Ensure that the supplier can provide timely deliveries at competitive prices without compromising quality.
Utilizing Plastic Injection Molding Supplies for Business Growth
For businesses involved in manufacturing, particularly in sectors such as metal fabricators, effectively utilizing plastic injection molding supplies can be a catalyst for growth. Here are some strategies to consider:
1. Innovate with Design
Leverage advanced plastic injection molding techniques to explore innovative designs that can distinguish your products from competitors. Collaborating with skilled designers can yield breakthrough ideas that increase market appeal.
2. Streamline Production Processes
Utilize automation and better machine maintenance practices to enhance efficiency. Regularly assess your production line and invest in improvements that can reduce downtime.
3. Optimize Material Usage
By choosing high-quality raw materials and implementing precise molding techniques, you can reduce waste and lower production costs, ultimately increasing profit margins.
4. Expand Product Lines
Invest in multi-cavity molds to expand your product offerings without a significant increase in production costs. This can enable your business to reach a wider customer base.
Future Trends in Plastic Injection Molding Supplies
The plastic injection molding industry is continually evolving, with advancements in technology and material science shaping its future. Here are some trends to watch:
- Increased Use of Recycled Materials: Sustainability is becoming a priority, and incorporating recycled materials will help reduce environmental impact.
- Smart Manufacturing: The integration of IoT and automation in plastic injection molding machines is expected to increase efficiency and provide better data analytics.
- 3D Printing Integration: The combination of 3D printing and injection molding is creating new possibilities for rapid prototyping and custom mold design.
- Advanced Simulation Software: Investment in software that simulates mold flow can enhance mold design and reduce production errors.
Conclusion
In conclusion, the realm of plastic injection molding supplies is vast and critical to successful manufacturing processes. For businesses in the sector, understanding these supplies, prioritizing quality, and leveraging them to enhance production can lead to remarkable growth and sustainability. By staying abreast of trends and continually seeking improvement, companies like Deep Mould can secure their place as leaders in the competitive landscape of metal fabricators and plastic injection molding. Always remember that investing in quality supplies is not just a cost but a strategic advantage that paves the way for future success.